PROCESS CHAIN STANDARDS
Quality Control
Quality control processes result in improving and guaranteeing customer satisfaction, complying with established standards, thus building customer confidence and strengthening the brand’s reputation. It also guarantees operational efficiency, since the early identification of defects or irregularities through quality controls allows timely corrections, avoiding rework and reducing waste of resources. This leads to a more efficient supply chain and lower operating costs.
At Tech id we study the processes to achieve excellence in their execution in the broadest sense, and we manage adequate control systems in each one of them, applying appropriate technologies in each case.
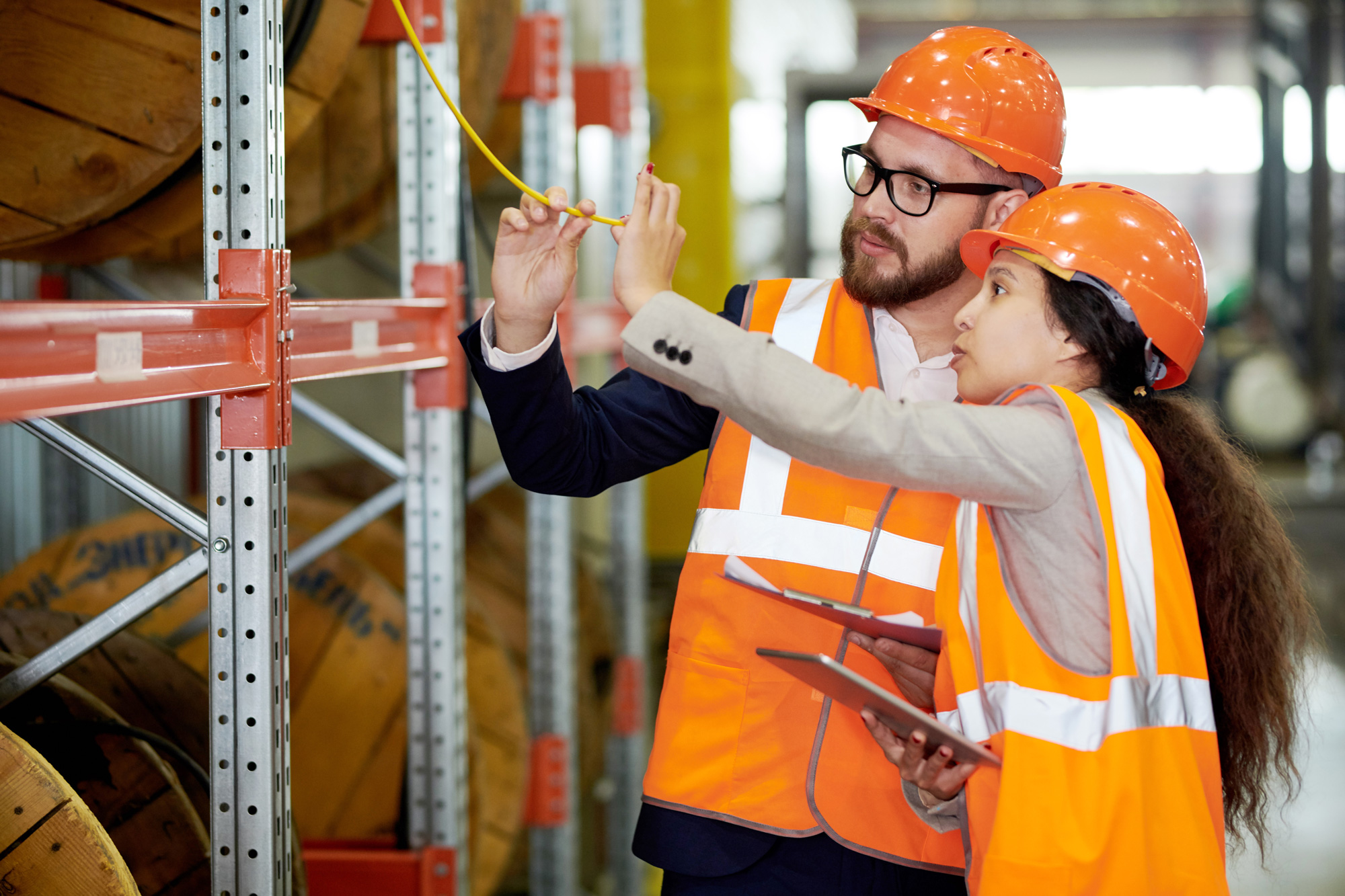
Advanced Quality Control Processes
In production, the use of advanced technologies: intelligent sensors, computer vision systems, machine vision and above all the analysis and management of data in real time, enhances the ability of quality control to identify and correct problems proactively.
In logistics environments it is essential to be sure that each link in the chain is correctly executed, since subsequent processes are based on the fact that upstream there are tasks that have already been performed, and in order not to repeat tasks they are assumed to be correct.
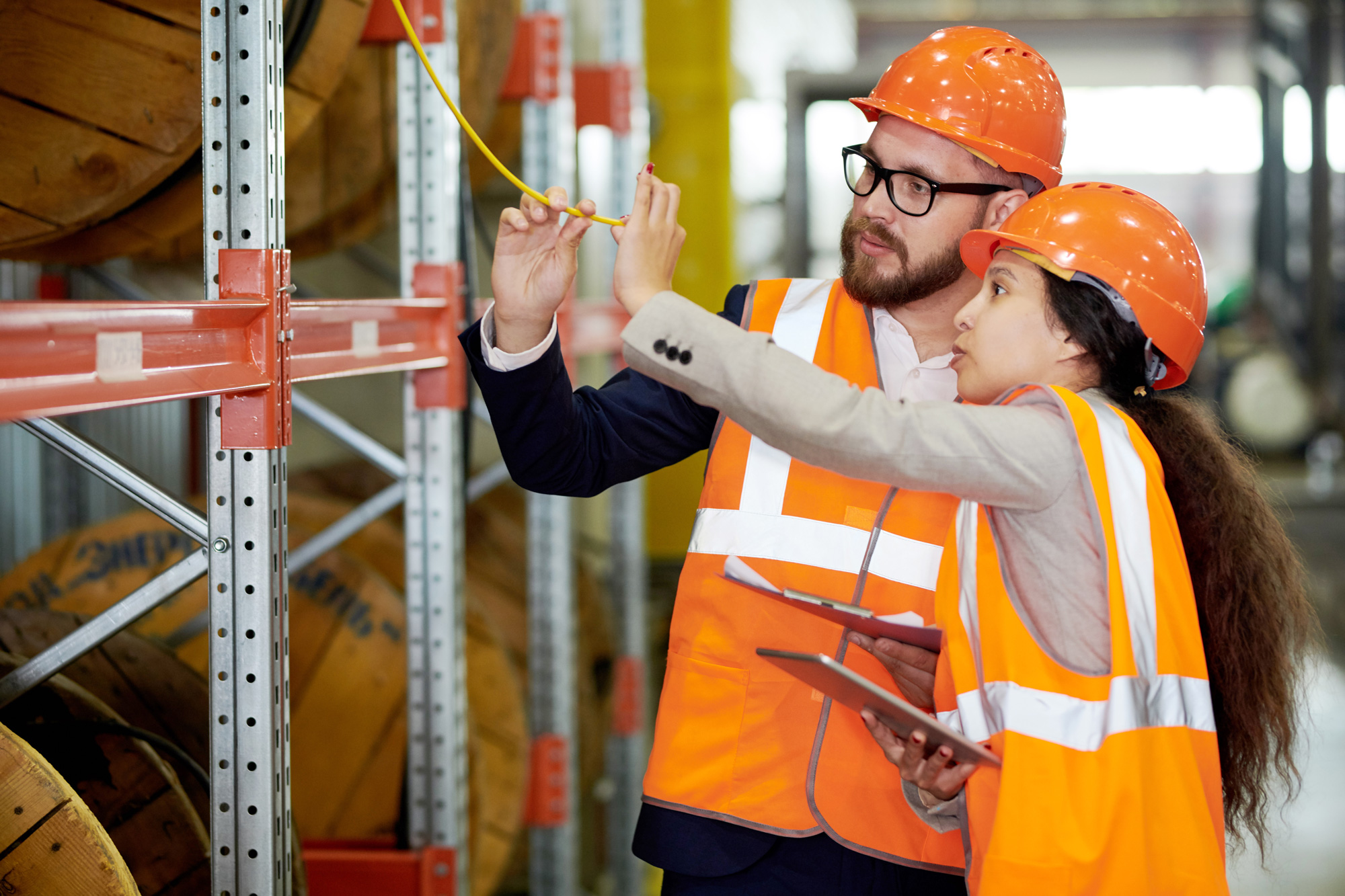
Receiving and Storage
Tracking of Routes and Conditions of Transportation
Returns Management
Therefore, automation of processes and tasks contributes to greater accuracy and speed and thus minimizes the need for quality controls.
Finally, of course, data analytics: Data analysis allows for the identification of patterns and trends, facilitating continuous improvement and anticipation of potential quality issues.
Benefits of Implementing Quality Control in Businesses
-
Cost Reduction:
Process optimization is always synonymous with cost reduction. Achieving optimum quality is the goal of any optimization and automation process. Quality controls will always be defined according to the process and possible errors.
-
Improve service and customer experience
By optimizing your tasks and certifying your product you will always get closer to the customer, the price positioning for the product or service must be in accordance with the quality delivered and/or provided.
-
Improve inventory quality
Ensuring the correct management of warehousing processes will always prioritize inventory quality.
-
Optimizes the planning of the rest of the processes
The digitization of the execution of processes in real time in your management systems or corporate systems offers the possibility of reviewing the planning and prioritization of the tasks to be performed based on reality and not on an initial planning.
-
Operational Efficiency
The operation of a well-coordinated supply chain is always based on not repeating tasks already performed in previous links. Having the assurance that upstream processes are correctly executed and information sharing is consistent is the basis for an integrated, collaborative and therefore efficient supply chain.
-
Sharing and visibility in your supply chain
The goal of optimizing the supply chain greatly benefits all links in the chain itself, and that optimization involves sharing processes and information. That is why having the right information in corporate or management systems is defined as a critical task for any company. Your company will obtain a differential value in terms of its ability to collaborate and integrate with its customers and suppliers, sharing quality information.
-
Greater security in management and business decision making:
The automated digitization in real time of the information generated by the process itself ensures that this information is complete and accurate, in addition to having it available in the appropriate systems, whether it is a WMS or an ERP. This makes it possible to make executive or strategic decisions in a secure way, offering the possibility of working with dashboards, KPi's, etc.
-
Cost Reduction:
Process optimization is always synonymous with cost reduction. Achieving optimum quality is the goal of any optimization and automation process. Quality controls will always be defined according to the process and possible errors.
-
Improve service and customer experience
By optimizing your tasks and certifying your product you will always get closer to the customer, the price positioning for the product or service must be in accordance with the quality delivered and/or provided.
-
Improve inventory quality
Ensuring the correct management of warehousing processes will always prioritize inventory quality.
-
Optimizes the planning of the rest of the processes
The digitization of the execution of processes in real time in your management systems or corporate systems offers the possibility of reviewing the planning and prioritization of the tasks to be performed based on reality and not on an initial planning.
-
Operational Efficiency
The operation of a well-coordinated supply chain is always based on not repeating tasks already performed in previous links. Having the assurance that upstream processes are correctly executed and information sharing is consistent is the basis for an integrated, collaborative and therefore efficient supply chain.
-
Sharing and visibility in your supply chain
The goal of optimizing the supply chain greatly benefits all links in the chain itself, and that optimization involves sharing processes and information. That is why having the right information in corporate or management systems is defined as a critical task for any company. Your company will obtain a differential value in terms of its ability to collaborate and integrate with its customers and suppliers, sharing quality information.
-
Greater security in management and business decision making:
The automated digitization in real time of the information generated by the process itself ensures that this information is complete and accurate, in addition to having it available in the appropriate systems, whether it is a WMS or an ERP. This makes it possible to make executive or strategic decisions in a secure way, offering the possibility of working with dashboards, KPi's, etc.
May we help you?
- +34 91 430 47 82
- info@tech-id.com
Telephone: 039 51 58 592
E-mail: info@tech-id.com
Address: Fuencarral, 44
28018 Alcobendas (Madrid)
Phone: +34 6 17 46 02 27
E-mail: info@tech-id.com
Address: Calle Calatrava 23, Barcelona
Phone: +39 011 18 98 3679
E-mail: info@tech-id.com
Address: Via Migliarone, 21/A
10091 – Alpignano (TO)
Phone: +39 039 51 58 592
E-mail: info@tech-id.com
Address: Via Berlinguer, 18
20872 – Cornate d’Adda (MB)
Telephone: 039 51 58 592
E-mail: info@tech-id.com
Address: Fuencarral, 44
28018 Alcobendas (Madrid)
Phone: +39 011 18 98 3679
E-mail: info@tech-id.com
Address: Via Migliarone, 21/A
10091 – Alpignano (TO)
Phone: +39 039 51 58 592
E-mail: info@tech-id.com
Address: Via Berlinguer, 18
20872 – Cornate d’Adda (MB)
Find the solution to automate and optimize your processes and integrate all your corporate information. Ask us and together we will analyze your case.